The CNC milling machine
with impressive performance
for milling aluminium
This water-cooled CNC milling machine mills aluminium with two axis groups and two milling spindles. As the unit is equipped with two machining tables, the milling machine can be operated in alternation. The CNC machine is much lighter and cheaper than a comparable machine tool.
Highly dynamic CNC milling machine for aluminum
The generous dimensions of the CNC milling machine and the comparatively long working tables allow a great deal of flexibility with components of different sizes. Thanks to the integration of two independent axis groups and two milling spindles, the CNC machine is noted for its high throughput and machining speed. The CNC machine gives you the option either to mill a single component using both axis groups or to machine two different components on a single table or on two separate tables.
This application and the transfer of our expertise in plastics technology has enabled the development of an extremely flexible and highly dynamic CNC milling machine for aluminium that makes the best use of the material.
Significantly more cost-effective than machines for steel processing
This is why the CNC milling machine is comparatively light and much cheaper compared to machines that are designed specifically for machining steel. The transmissions that are used allow rapid positioning and the rotary axes can be aligned quickly. Thanks to the reduced weight, the CNC machine reaches the programmed positions in record time. The precision of the CNC milling machine is exceptional and is also supported by the different compensation options. These include throughput compensation, spindle pitch compensation and VCS rotary compensation. This combination ensures accurate machining and the highest quality standards in production.
Flexibility regarding customer-specific customizations
In contrast to conventional steel-processing machines, the CNC machining centre is noted for the considerable flexibility it offers in accommodating customer-specific adjustments. This relates to aspects such as the design, dimensions, length and the available options of the CNC machine. The robust design made from micro-finished steel makes it possible to deliver the CNC milling machine cost-effectively even for intricate solutions in customised machine construction. With this CNC milling machine, it is possible to switch between materials smoothly at any time, for example from aluminium to plastic.
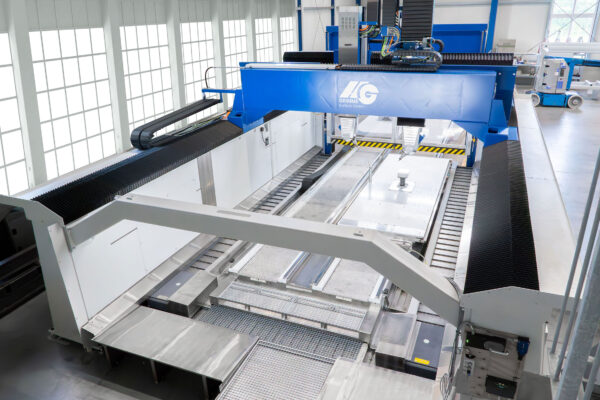
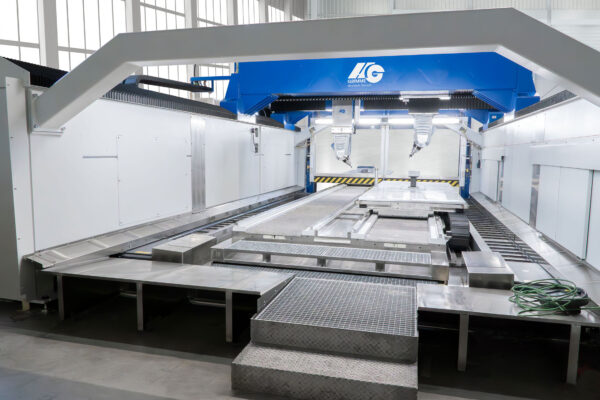
Insight into the equipment of the CNC machining center
The Tables
The component dimensions for a single table are X 4050 mm, Y 1300 mm and Z 800 mm (figure at top). When the two tables are joined together, the dimension of the Y axis is increased to 2700 mm. Each table has a loading capacity of up to 1600 kg. Depending on the distance from the shuttle table, the tables can be moved at a speed of 50 m/min, even at up to 80 m/min out of the CNC machine. The feeding of the shuttle tables takes place outside the CNC machining centre.
If the components are heavier, there is the option of fitting a fixed table. This can be fitted using a crane or other lifting equipment.
Thanks to its modular design, the size of the CNC milling machine is variable. It is possible at any stage to add a tower in order to expand the travel path in the X direction as you require. This means a CNC machine for extremely large components can be developed at any time.
The milling spindles
The two spindles of the CNC machine have an impressive peak output of 18 kW. The milling tool is cooled via two AKZ nozzles. The spindles reach a top speed of 24,000 revolutions per minute, although they maintain an impressive nominal torque of 23 Nm even at low speeds.
The clevis with the A and C axes is equipped with an external encoder to achieve exceptionally precise milling results. The encoder guarantees particularly precise positioning. The milling spindle itself also has an encoder that enables absolutely precise positioning. This is particularly important for thread cutting applications.
Tool changer
The tool changer, designed to the HSK F 63 standard, comprises a disc-type magazine with 10 tool slots for each axis group. The tool magazine has a flexible design so that a second disc-type magazine can be integrated in the same housing. This version means that for each axis group with a milling spindle a total of 20 tools are available directly in the CNC milling machine. The tool changer can be positioned on the left or right side depending on the accessibility from the outside. Using tool magazines on both sides of the CNC machine increases the total capacity to an impressive 80 tools.
The tool changers are easy to access from the outside and can be populated even while the CNC machining centre is operating. Special sensors allow the CNC machine to automatically detect which tools have been inserted and whether a slot is already occupied. In addition, programming and fitting of spare tools in the magazine allows the machine to work in optimised fashion. If a tool becomes worn, the CNC milling machine automatically switches to the next available spare tool.
Chips and coolant
The CNC machine can be operated either with a minimal amount of lubrication or with splashing water. The use of air-atomised oil, in other words a minimal amount of lubrication, is suitable for many different applications. This applies, for example, to machining freeform surfaces and in some cases is also sufficient for machining aluminium. However, splashing water or cooling water is also available if necessary. This is the case, for example, when drilling deep holes or drilling hollow forms out of aluminium.
The external cooling means that deep drill holes can also be efficiently rinsed out and cleaned. Thanks to the ingenious cooling process and the appropriate coolant, it is possible to use standard tools without cannulations, which means there is no need for expensive alternatives. HG Grimme SysTech fits durable hydraulic pipes for the purpose of conveying the coolant through the machine.
The cooling water and chips are carried away by built-in transverse conveyors, longitudinal conveyors and water collection trays. The cooling water flows through the chain conveyor, where it is then pumped into a filtration unit, cleaned and reused. This ensures that the water is continuously recycled.
Optimum tolerances and precision
The CNC machine achieves the ultimate level of precision by implementing more Heidenhain linear measuring systems in the linear axes. Barcode scanning is used to record the status of the axes, avoiding and compensating for possible inaccuracies such as backlash or hysteresis. This produces a loss of precision in the travel path owing to the transmission or the weight of the axes. The precise information on the precise position is sent directly to the spindle, which can then be positioned exactly.
Control system, interfaces and data
The CNC milling machine is controlled by a Siemens 840d Solution Line control system, although there is also the option to use the Sinumerik ONE version. An OPC UA interface can be set up for the purpose of documenting the milling, process and machine data. A special Siemens licence allows all the required parameters and data to be accessed autonomously from the CNC machine. The freely programmable interface is provided directly ex works. This means required information can easily be recorded and read.
Alternatively, we offer the option of providing all the required information in a data block. This contains all the required specifications such as machining time, barcode, program, the tools used and much more. This data is accessed via the specified data block. The collected information is made available and can be downloaded.
Compact-sized solution, the small and space-saving machine:
We also offer more compact versions of the CNC milling machine with exactly the same functions. The smaller model with a gantry design does not feature a shuttle table and uses a slot table instead. Here too it is possible to use a transverse conveyor that collects and processes chips and water.
The CNC milling machine operates with a minimal amount of lubrication. It includes an oil mist separator, which makes it possible to mill different materials that do not require any cooling. A retractable roof ensures that the oil mist does not spread around the factory hall, but is instead collected within the CNC machine and extracted. The purified air is emitted into the hall or channelled outside, whereas the condensate is fed back into the circuit and filtered.
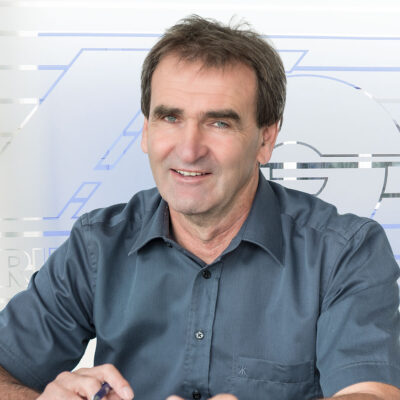
Training, maintenance, or technical support?
We have a global network of service centres and support partners that are trained on the relevant CNC machine. Our service engineers are able to speak the language of the country they are working in. Each CNC machining centre is equipped with remote maintenance routers. We can resolve many questions and issues with our remote maintenance support. In addition, our service team is on hand to support the engineers on site using remote maintenance. If necessary, our service team can also call on expert professionals from various departments like design, assembly or programming to ensure the optimum solution can be found.
Wolfgang Grimme | HG GRIMME SysTech
Various examples of aluminium machining applications
This CNC milling machine can be used to produce dedicated milling fixtures from materials such as Ureol or moulds from aluminium without needing to invest in expensive metalworking machinery. The machine also allows you to trim other materials such as plastics, composites and modelling materials.
Aluminium is frequently used to construct lightweight designs that are needed in the aviation and automotive industries, for example. Housings and covers are also made from aluminium, including housings for electronic devices, protective covers and machine parts. Aluminium is also widely used in prototyping. In the aviation industry, aluminium is used to make aircraft wings, fuselage components and landing gear. In the automotive sector, aluminium components can be found in engine blocks, transmission parts, frames and parts of the bodywork. Aluminium is used in the electronics industry to manufacture heat sinks, enclosures and structural components. In the construction industry, lots of architectural features such as claddings, railings, door frames and window frames are made from aluminium. Aluminium can even be used with great benefit in boat building and marine components because it is corrosion-resistant. It is used for boat hulls, masts or rudders.
The CNC milling machine has been developed for industry and all its applications and can be adapted in a modular fashion. If these possible adaptations are not sufficient to meet the requirements of the particular application, we can also draw on our wealth of expertise in customised machine construction.
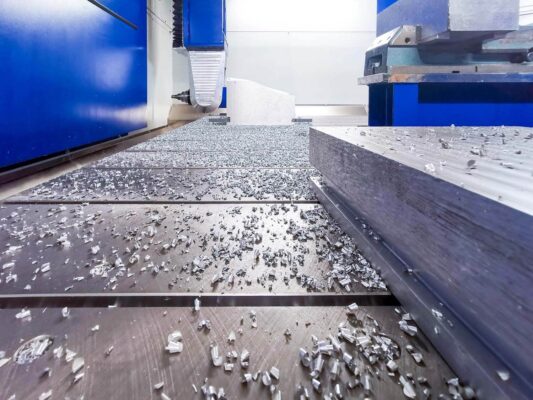
Sectors & Industries
Case Studies
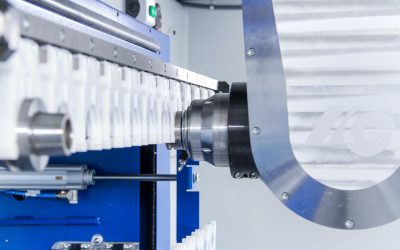
Aluminium machining in the model making sector – CNC milling machine
Symbolising the progress that has been made in aluminium machining
More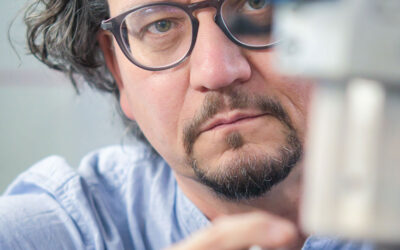
Teamwork when it comes to natural fibres
Germa Composite and HG GRIMME SysTech: Teamwork when it comes to natural fibres - CNC-Gantry milling machine for machining plastics and composite materials
More